Comment choisir les caillebotis ?
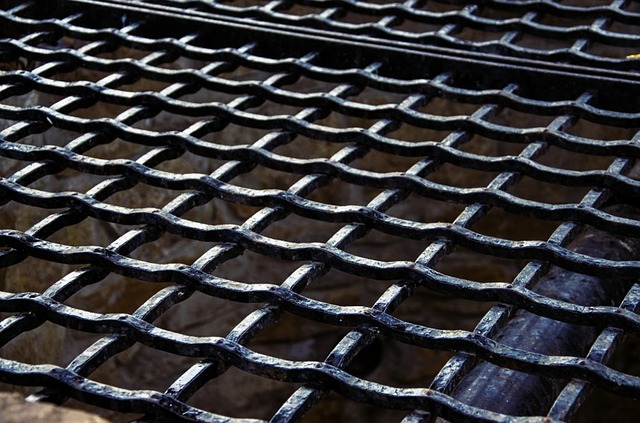
Les caillebotis en acier sont l’un des éléments structurels les plus utilisés, car ils allient légèreté, robustesse et prix abordable. Toutefois, il faut toujours garder à l’esprit qu’ils peuvent varier considérablement, même à l’intérieur de leur propre fourchette étroite. Les différentes variantes ont des propriétés légèrement différentes, de sorte que, selon l’usage auquel elles sont destinées, une variante particulière peut être plus ou moins performante. Afin de choisir la meilleure solution pour vous, il est utile de connaitre comment choisir les caillebotis et que faut-il prendre en compte lors de leur achat ?
Comment choisir les caillebotis ?
Pour choisir la taille et l’usage d’une grille, il faut tenir compte de sa conception et de ses dimensions. La longueur du caillebotis est déterminée par les plats de support, qui influencent la charge maximale. Plus les barres plates sont hautes et épaisses, plus le caillebotis est robuste. Ces barres plates doivent être soutenues des deux côtés. Leur hauteur détermine la longueur minimale du support, qui ne peut toutefois pas être inférieure à 30 mm. La largeur de la grille est déterminée par les barres plates ou les barres transversales et la résistance de la grille est assurée par les plats porteurs. Il faut également faire la distinction entre la taille des mailles et la taille de l’ouverture. La première est déterminée par la distance entre les barres/barreaux plats, la seconde par l’espace entre les murs de la structure sur laquelle repose le caillebotis, l’ouverture doit être de 4 à 8 mm plus grands que celle-ci. Entre deux supports, on calcule la portée du caillebotis. En ce qui concerne la méthode de fabrication, on distingue les caillebotis soudés, pressés et profilés.
Caillebotis soudés
Les premiers sont fabriqués en soudant ensemble des barres et des plats et sont fabriqués en acier galvanisé ou en acier inoxydable. En fonction de la taille des mailles, on compte environ 600 à 1000 joints par mètre carré d’un tel caillebotis. L’ensemble est relié par un cadre soudé, ce qui rend le caillebotis stable et résistant. Grâce à la technologie dans laquelle ils sont fabriqués, ils peuvent atteindre un large éventail de tailles, ils sont donc souvent utilisés comme plateformes. Parmi les caillebotis soudés, on trouve les caillebotis standards (RH), les caillebotis antidérapants (dentelés) et les caillebotis à maille plus dense, appelés offshare, qui, grâce à des barres supplémentaires, sont protégés contre la chute de petits objets.
Caillebotis pressés
Les caillebotis pressés sont constitués de barres plates et de barres transversales porteuses assemblées par soudage à froid. Tout d’abord, la bande est déroulée et coupée uniformément, puis les plats de support sont pressés avec une pression de plus de 100 tonnes dans les coupes coniques des plats transversaux. Comme les caillebotis soudés, ils peuvent avoir une surface standard antidérapante ou être renforcés pour résister à des charges très élevées. Parmi les caillebotis pressés, il existe également des caillebotis pleins, caractérisés par l’utilisation de barres plates identiques, perpendiculaires les unes aux autres. Ils sont souvent utilisés comme pare-soleil ou clôtures et, grâce à la possibilité d’un revêtement en poudre, également comme éléments décoratifs. Pour les caillebotis pressés, outre l’acier ordinaire, on utilise également l’acier inoxydable et l’aluminium.
Caillebotis profilés
Nous obtenons des caillebotis profilés à partir de matières premières similaires. Ils se distinguent des produits soudés et extrudés par le fait que leur surface est couverte de trous ronds et non rectangulaires. Grâce à leur construction, ils sont résistants à l’humidité et ont des propriétés antidérapantes.